The BASIC OXYGEN STEEL (BOS) - making
Process
This can be described via the following steps:
The process occurs in a furnace which is a specially designed
steel vessel that may be rotated through 360 in a vertical
plane.
The vessels are lined with heat resistant (refractory) materials
eg.dolomite (MgCO3/ CaCO3) and magnesite
(entirely MgCO3). These last for up to 2 weeks before
they have to be replaced.
- 1) Scrap steel is placed in the vessel followed by molten
iron directly from a
blast furnace.
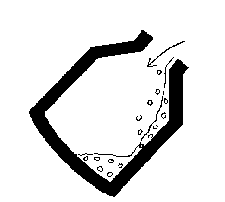
- 2) the vessel is stood upright and a water-cooled lance is
lowered from above and oxygen is blown onto the surface at high
speed. Carbon in the iron is oxidised to CO and
CO2:
C(S) + O2(g) > CO2(g)
CO2(g) + C(S) > 2CO(g)
2CO(g) + O2(g) > 2CO2(g)
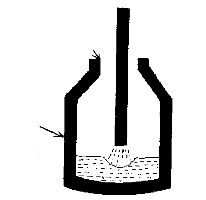
- 3) After a few minutes the oxygen is stopped. A flux of
calcium fluoride (fluorspar, CaF2) and "burnt lime"
(CaO) is then added.
Burnt lime is calcium oxide formed by heating calcium carbonate
until it decomposes:
CaCO3(s) > CaO(s) +
CO2(g)
This is introduced as a method of removing unwanted Si and P,
since:
4P + 5O2 >
P4O10
6CaO + P4O10 >
2Ca3(PO4)2
Si + O2 > SiO2
CaO + SiO2 > CaSiO3
this produces a slag.
Manganese is oxidised but remains in the iron, sulfur dissolves
in the slag and is removed.
- 4) the lance is lowered again for another blow of oxygen, the
vessel contents are analysed to see whether step 3 should be
repeated.
If all is OK then:
- 5) the vessel is tilted and the steel is tapped off below the
slag level
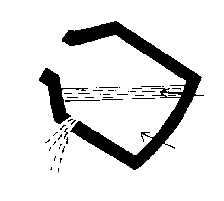
- 6) the slag is removed by tilting the vessel in the opposite
direction.
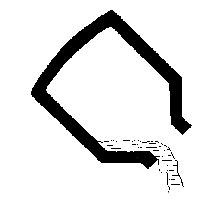
- The whole cycle takes about 45 minutes.
Types of Steel
In general, steels can be divided into 2 groups:
Carbon Steels
small % of C (0.03 to 1.5%),
residual amounts of other metals
comprises 90% of all steels produced
At high temperatures, 907-1400 C, Fe is cubic close-packed
(ABCABC) and can hold 1 C for every 12 Fe atoms.
This form of steel is called 'austenite'.
With excess carbon, an interstitial steel is produced called
'cementite' which has a precise composition of
Fe3C.
'austenite' is stable down to 690 C where it converts
to:
a body centred form called 'ferrite' which has less
carbon and also 'cementite'.
It is possible to retain the 'austenite' structure below
690 C by adding Mn.
Alloy Steels
contain C and controlled amount of other metals; eg Mn, Cr, Ni, Mo.
- C with increasing C content, hardness and
tensile strength
increases, but ductility and welding properties
decrease
- Mn increases strength and hardness, but
less effective than C
good for high energy impact, battering - rifle barrels
etc.
- Cr improves corrosion and abrasion
resistance
- Ni increases toughness, tensile strength,
hardness and corrosion resistance
- Mo increases hardness and tensile
strength especially at high temperatures
return to the C21J course
outline
Return to Chemistry, UWI-Mona,
Home Page
Copyright © 2005 by Robert John
Lancashire, all rights reserved.
Created and maintained by Prof. Robert J.
Lancashire,
The Department of Chemistry, University of the West Indies,
Mona Campus, Kingston 7, Jamaica.
Created July 2000. Links checked and/or last
modified 20th October 2005.
URL
http://wwwchem.uwimona.edu.jm/courses/BOS.html